In the realm of industrial machinery, understanding the components and functionalities of steam boilers is crucial for maintaining efficient operations. Steam boiler systems play an integral role in various industries such as power generation, manufacturing, and even in residential heating solutions. This article delves into the essential parts of steam boilers and their functions, offering insights grounded in industry expertise.
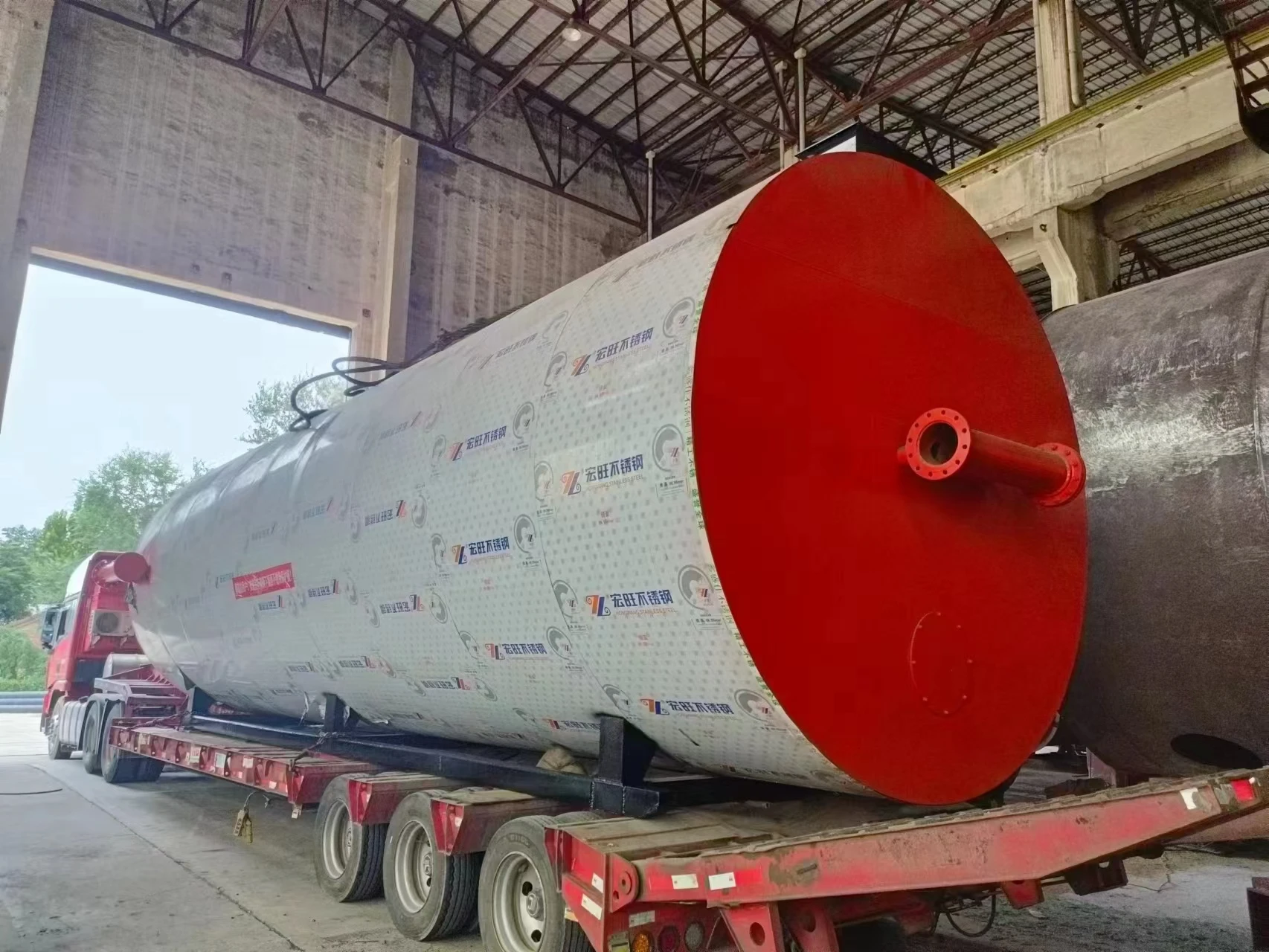
1. Boiler Shell The boiler shell acts as the primary container that withstands internal pressure from the steam. It's typically made of high-grade steel to ensure durability and safety.
The boiler shell houses various other components crucial for effective steam production.
2. Furnace Also known as the combustion chamber, the furnace is where fuel combustion occurs. It provides the necessary heat to convert water into steam. High-quality insulation in the furnace walls is essential to maximize energy output and reduce heat loss, thereby ensuring efficient fuel usage.

3. Burner The burner is a critical component that initiates the combustion process. It mixes fuel with air and ignites the mixture. Proper adjustment and maintenance of the burner are vital to achieve complete combustion and minimize emission levels, enhancing the boiler's performance and environmental compliance.
4. Water Tubes/Fire Tubes Depending on the boiler type, water or fire tubes serve as the primary heat exchange pathways. Water-tube boilers have water flowing through tubes heated externally by combustion gases, while fire-tube boilers have gases flowing through tubes submerged in water. The choice between the two impacts the boiler's efficiency, pressure handling, and application suitability.
5. Steam Drum In water-tube boilers, the steam drum is an essential separator between water and steam. It acts as a reservoir where steam is collected and separated from water, ensuring consistent steam supply while maintaining water levels for optimal heat exchange.
6. Superheater Not all steam boilers have a superheater, but those that do significantly improve steam quality. Superheaters increase the temperature of the steam beyond its saturation point, enhancing energy transfer efficiency and reducing condensation-related issues.
steam boiler parts and function pdf
7. Economizer The economizer is a component that preheats the feed water using residual flue gases. This process effectively recycles energy, reducing fuel consumption and increasing the overall efficiency of the boiler system.
8. Safety Valves These valves are essential for preventing pressure build-up beyond safe levels within the boiler. They automatically release steam when pressures exceed predefined limits, ensuring the safety of personnel and equipment.
9. Feed Water Pump The feed water pump's function is to maintain a constant level of water within the boiler. Precise control of feed water flow is crucial for the stability of steam production and the prevention of pressure fluctuations.
10. Blowdown Valve Regular removal of sediment and impurities from the boiler is managed through blowdown. The blowdown valve allows operators to expel concentrated water and particulate matter, aiding in the prevention of scale and corrosion, which can significantly impair boiler efficiency and lifespan.
11. Control Systems Modern steam boilers are equipped with advanced control systems that manage pressure, temperature, and water levels. These systems utilize sensors and automated feedback loops to optimize performance, ensuring reliable and efficient operation.
Understanding the intricate workings and maintenance of these components is paramount for anyone involved in the operation or maintenance of steam boiler systems. Proper upkeep not only extends the lifespan of the equipment but also ensures safety and operational efficiency. For industries reliant on steam generation, investing in a knowledge base about steam boiler parts and functions is a step toward sustainable and cost-effective production processes.