Steam boiler corrosion is a critical concern in industrial applications, impacting efficiency, safety, and the lifespan of the equipment. Understanding the causes and implementing preventive measures are essential to mitigate risks and maintain optimal boiler performance.

Corrosion in steam boilers is primarily caused by the interaction of metal surfaces with oxygen, water, and other substances. This interaction leads to the deterioration of boiler materials, resulting in leaks, scaling, and ultimately, system failure. The presence of dissolved oxygen in feed water is a significant contributor to the corrosion process, particularly in high-temperature environments where the reaction rate increases.
The two main types of corrosion affecting steam boilers are uniform corrosion and localized corrosion. Uniform corrosion occurs evenly across metal surfaces, often leading to gradual thinning of the material. In contrast, localized corrosion, including pitting and stress corrosion cracking, focuses on specific areas, creating more severe damage at concentrated points.
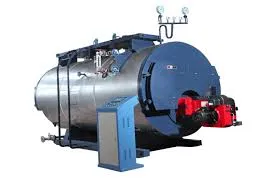
One effective strategy to combat corrosion is through the use of oxygen scavengers. Chemicals like sodium sulfite or hydrazine are commonly added to boiler feed water to neutralize dissolved oxygen. By reacting with the oxygen before it can interact with the boiler metal, these scavengers reduce the potential for corrosion. Additionally, ensuring proper deaeration of feed water by mechanical means, such as a deaerator, can significantly reduce oxygen levels.
Another vital aspect is maintaining proper pH levels within the boiler system. Acidic conditions accelerate the corrosion process; therefore, feed water should be maintained at a slightly alkaline pH. The use of alkaline chemicals, such as sodium hydroxide, helps buffer the water and protect metal surfaces from acidic attack.
Water treatment programs tailored to the specific needs of a steam boiler system play a crucial role in preventing corrosion. These programs should be designed by water treatment specialists after a thorough analysis of the water chemistry, boiler design, and operational parameters. Regular monitoring and adjustment of the water treatment regimen ensure ongoing protection against corrosion.
steam boiler corrosion
Implementing a rigorous maintenance routine is essential to identify early signs of corrosion and address them promptly. Routine inspections, including non-destructive testing methods such as ultrasound or radiography, help detect internal damage before it manifests visibly. Early detection through regular maintenance allows for targeted repairs, preventing minor issues from escalating into costly damage.
Advanced coatings and materials can provide an additional layer of protection against corrosion. Epoxy coatings or specialized alloys with increased resistance to chemical degradation offer enhanced durability in corrosive environments. Selecting the appropriate materials based on the boiler's operating conditions and the nature of the substances involved is crucial for long-term performance.
Operational modifications can also play a vital role in reducing the risk of corrosion. Controlling the boiler's temperature and pressure within optimal ranges minimizes stress on components, reducing the likelihood of corrosion-related failures. Additionally, ensuring consistent fuel quality and using additives to stabilize combustion can mitigate the formation of corrosive byproducts.
Training and educating personnel on the causes and prevention of steam boiler corrosion foster a culture of preventative maintenance. Operators and maintenance staff equipped with the knowledge to identify potential issues and respond effectively contribute to the longevity and reliability of boiler systems.
In summary, steam boiler corrosion is a multifaceted challenge requiring a comprehensive approach encompassing chemical treatments, material selection, maintenance strategies, and personnel training. Through a combination of these measures, industries can significantly extend the lifespan of their steam boilers, optimize performance, and maintain safe operations. Emphasizing a proactive approach to corrosion prevention ensures the sustainable and efficient use of boiler technology, ultimately contributing to the economic and environmental goals of industrial operations.