Adjusting the water level in a steam boiler is a critical maintenance task that ensures the safety and efficiency of your boiler system. Proper management of the water level prevents potentially dangerous situations such as overheating, dry firing, or even explosions. Whether you're a seasoned engineer or a facility manager, understanding the intricacies of water level adjustment and control can enhance both performance and equipment longevity.
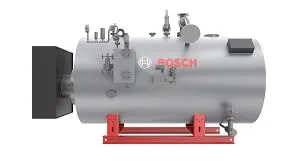
The water level in a steam boiler must align within specified operational levels to maintain a consistent steam output. This is dictated by the nature of the steam production process, where the correct amount of water must come in contact with the heated surfaces to convert into steam efficiently.
Firstly, it’s important to recognize the significance of maintaining the recommended water level within the boiler drum. Operating with too little water can expose tubes to excessively high temperatures, leading to tube failure. On the other hand, too much water can impair the separation of steam and water, causing poor efficiency and carryover of water into the steam system, both detrimental to the operations.

To start the adjustment process, ensure the boiler is off and cooled down to avoid safety hazards. Equip yourself with appropriate personal protective equipment (PPE) as an extra measure.
Begin by inspecting the gauge glasses which provide a visual indicator of the water level inside the boiler. It's prudent to clean these glasses and verify their accuracy regularly.
Next, examine the feedwater system. The water level is primarily adjusted by altering the feedwater flow into the boiler drum. Modern boiler systems often employ automated level control systems—typically a three-element control system is utilized in industrial settings, which balances drum level, steam flow, and feedwater flow. However, even automated systems require initial manual calibration and periodic maintenance checks to ensure functionality.
Manual adjustment involves using the feedwater valve to increase or decrease flow. Carefully observe the level rise or fall in response to these adjustments. A slow, deliberate process is essential to avoid overshooting the desired level. Maintain vigilance for any changes in pressure, as fluctuating levels can greatly affect system pressure and stability.
how to adjust water level in steam boiler
Accurate measurement instruments are crucial for this task. Certified level sensors and transmitters can greatly enhance precision in monitoring. However, in cases of discrepancies between sensor data and gauge readings, a thorough investigation is necessary to eliminate errors.
In environments where automation is present, operators should be familiar with the controls and understand the operation of Programmable Logic Controllers (PLCs) or Distributed Control Systems (DCS), which manage the water level. These systems offer enhanced control but require expertise to troubleshoot and adjust where necessary.
Moreover, training and certifications for boiler operation are not merely legal prerequisites; they empower operators with the knowledge necessary to intuitively manage complex systems. An operator armed with a robust understanding of thermodynamics and fluid dynamics is distinctly more effective at maintaining optimum operational conditions.
Safety cannot be underestimated. Regular safety audits and drills ensure the team is prepared for any unintended deviations in the system. Consider employing redundant systems such as low-water cutoffs and automated blowdown systems for additional safety layers.
In conclusion, adjusting the water level in a steam boiler requires a blend of technical expertise, practical experience, and a commitment to safety. Understanding the interaction between water levels, boiler efficiency, and system safety prepares any operator or engineer to make informed decisions, thereby enhancing both operational uptime and safety. Proper training, regular maintenance, and leveraging advanced control systems are the keystones to mastering water level management in steam boilers.