An industrial steam system is one of the foundational elements in numerous manufacturing and processing industries. As an essential utility, it powers a myriad of machinery and processes, ensuring efficiency and productivity across the board. Understanding the intricacies of these systems can provide industries with significant cost reductions, enhanced operational efficiency, and increased reliability.
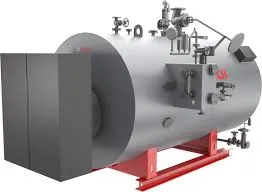
The backbone of an industrial steam system is the boiler. These sophisticated machines are responsible for turning water into steam, which then powers everything from turbines to heating systems. Modern boilers are marvels of engineering, designed with precision and crafted to meet the rigorous demands of industrial applications. They come equipped with state-of-the-art controls that allow for precision monitoring and adjustments, optimizing steam output while ensuring fuel efficiency.
The distribution of steam within an industrial facility is another critical area that requires attention. Steam traps, valves, and piping systems must be meticulously maintained to prevent leaks and ensure efficient transportation of steam. Steam traps, in particular, serve the crucial function of removing condensate and air without letting steam escape, thus maintaining energy efficiency. Regular maintenance and upgrades in these components are necessary to avoid disruptions and costly repairs.

Heat exchange is the heart of an industrial steam system. This process involves transferring heat from steam to another medium, such as water or air, maximizing the utilization of steam energy. Heat exchangers need to be tailored to specific industrial requirements, taking into account factors such as pressure, temperature, and the fluids involved in the process. Expertly designed heat exchangers improve thermal performance, reduce energy consumption, and increase overall system efficacy.
Condensate recovery is another vital aspect of steam system efficiency. By capturing and returning condensate to the boiler, industries can save on water and energy costs. This process significantly reduces the need for treated fresh water, decreasing operational costs. By using advanced condensate recovery solutions, industries not only enhance the sustainability of their operations but also improve their bottom line.
industrial steam system
The implementation of digital and smart solutions is transforming how industrial steam systems are managed. IoT-enabled analytics provide valuable insights into system performance, enabling predictive maintenance and minimizing downtime. By leveraging these technologies, industries can identify potential issues before they escalate, allowing for proactive problem-solving and efficient resource management.
Safety cannot be overlooked when discussing steam systems. The high pressures and temperatures involved necessitate stringent safety protocols. Regular safety inspections and compliance with international standards are paramount to ensuring safe operations. Trained personnel are indispensable in managing these systems, as they require expertise to navigate the complexities involved and prevent accidents.
Environmental sustainability has also become an integral consideration in the design and operation of industrial steam systems. By utilizing cleaner energy sources, such as natural gas and waste-to-energy technologies, industries can significantly reduce their carbon footprint. Moreover, energy-efficient design and operation contribute not only to a cleaner environment but also result in lower operational costs.
In conclusion, the industrial steam system remains an indispensable component of modern manufacturing and processing industries. Its effective management requires a blend of technical expertise, ongoing maintenance, and advanced technology integration. By focusing on these critical areas, industries can maximize efficiency, ensure safety, and embrace sustainability, ultimately achieving a competitive edge in their respective markets. While the fundamental principles of steam systems have remained consistent, the innovations and improvements in their components and management strategies continue to evolve, reflecting their indispensable role in industrial productivity.