Industrial hot oil heaters, also known as thermal fluid heaters, have revolutionized the way industries manage heat production. Offering remarkable efficiency, precise temperature control, and impressive reliability, these systems highlight their superiority over traditional heating methods. But why is this technology becoming the linchpin for countless industrial applications? Let’s dive into its extraordinary capabilities.
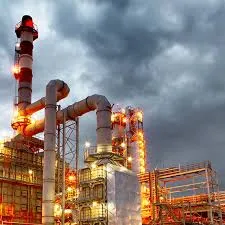
With the rise of energy costs and the ever-increasing need for efficiency, industries are in constant search for thermal systems that are both effective and economical. Hot oil heaters operate on a closed-loop system using thermal oils. This closed-loop design minimizes thermal loss and maximizes energy efficiency, which translates to reduced operational costs and lower environmental impacts.
One of the core strengths of industrial hot oil heaters is their ability to reach high temperatures with minimal pressure. Unlike steam systems that require high pressures to achieve the same temperature levels, thermal fluid heaters safely operate at atmospheric pressures. This distinction not only reduces the potential for system failures but also enhances workplace safety—a significant factor in industrial settings.

Experience with various industries has shown that thermal fluid systems offer unparalleled precision and uniformity in temperature control. This consistency is crucial in sectors such as plastics, pharmaceuticals, and chemicals, where small deviations can impact product quality. For example, in the plastics industry, accurate temperature management is essential for molding precision, making hot oil heaters a preferred solution.
From an expertise standpoint, the adaptability of industrial hot oil heaters sets them apart. They are engineered to support various heat transfer fluids—ranging from mineral oils to synthetic fluids—which can be tailored to the specific thermal demands of different industries. This versatility ensures that industries don’t have to compromise on their heating needs, making them invaluable across diverse applications including oil and gas processing, food manufacturing, and textile production.
industrial hot oil heater
The reliability of these systems is another compelling reason for their adoption. Designed with advanced technology to withstand prolonged operational hours and rigorous conditions, hot oil heaters exhibit unparalleled durability. Routine maintenance is simplified due to fewer mechanical components, reducing downtime and enhancing productivity. Many facilities report operational continuance over decades with minimal overhaul, underscoring trustworthiness and long-term cost savings.
The integration of advanced control systems further cements their authority in industrial heating solutions. These systems facilitate real-time monitoring and precision management of the heating process, ensuring peak performance. By incorporating smart technology, industries can optimize energy usage, predict maintenance needs, and prevent unexpected downtimes, optimizing production lines and enhancing overall efficiency.
Trust in industrial hot oil heaters is further augmented by the stringent international regulations and safety standards they meet. Manufacturers design these systems in accordance with protocols that ensure safe and reliable operations, building confidence and ensuring peace of mind for users across industries.
In conclusion, industrial hot oil heaters are a top choice for modern industries seeking effective, reliable, and efficient heating solutions. Their ability to deliver high-temperature outputs at low pressures, coupled with energy efficiency, precision, and reliability, positions them as an essential asset. By harnessing this technology, industries not only achieve operational excellence but also spearhead sustainability and safety, marking them as a cornerstone in progressive industrial practices.