Blowing down a steam boiler is a critical maintenance procedure that ensures the system operates efficiently and safely. This process involves discharging water from the boiler to remove accumulated impurities and maintain optimal water chemistry. Knowing how often to perform a blowdown can be the difference between a boiler running smoothly and one facing frequent issues or inefficiencies.

Understanding Blowdown Frequency
To determine how often to blow down a steam boiler, a few essential factors need careful consideration. Each boiler system is unique, magnifying the importance of not relying solely on generic advice but rather tailoring the blowdown schedule to fit the specific conditions and requirements of the operation.
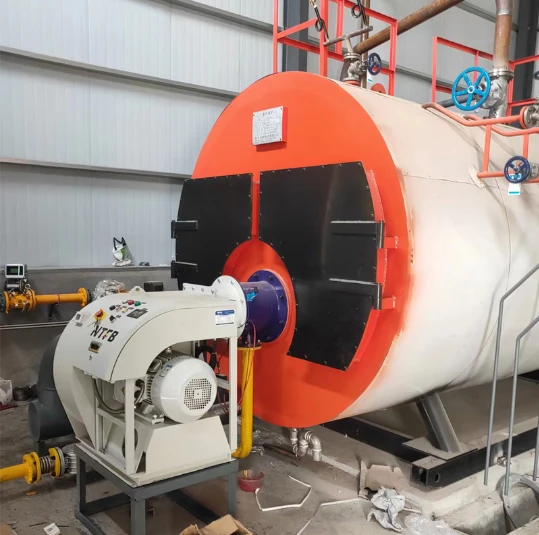
1. Water Quality and Its Crucial Role
The mineral content and hardness of the feedwater are primary determinants of blowdown frequency. High levels of dissolved solids and minerals can lead to scaling and corrosion, significantly reducing the boiler's efficiency and lifespan. In facilities where the water quality fluctuates or contains high amounts of impurities, more frequent blowdowns are necessary to maintain a stable system.
2. Boiler Type and Its Implications
The type of boiler in use also impacts how often a blowdown should occur. Fire-tube boilers and water-tube boilers, for instance, have different design and operation characteristics, influencing their susceptibility to sediment and scale buildup. Water-tube boilers, often used in high-pressure and large-scale operations, generally require more frequent blowdowns compared to fire-tube models.
3. Operating Pressure and Temperature
Higher pressure and temperature levels in boiler operations tend to accelerate the rate at which impurities precipitate out of the water. Therefore, boilers operating under high pressure often demand more frequent blowdown sessions to manage the concentration of solids effectively.
Expert Recommendations from the Field
how often should you blow down a steam boiler
Professional boiler operators often suggest initiating with daily blowdowns to establish a baseline for your particular system. This period of observation allows operators to closely monitor the accumulation rate of impurities and system performance, gradually adjusting the frequency based on observed conditions.
Conducting Tests and Analyses
Regular analysis of boiler water is essential in forming a precise blowdown strategy. Testing kits and periodic laboratory analyses provide vital data about the levels of total dissolved solids (TDS) and other pertinent parameters. By maintaining TDS within recommended limits, operators can optimize blowdown frequency, improving efficiency and preventing potential damage.
Balancing Safety with Efficiency
The safety of the boiler and plant personnel must be the guiding principle in determining blowdown frequency. Neglecting adequate blowdown schedules can lead to hazardous conditions such as pressure buildup and boiler failure. Conversely, excessive blowdowns waste energy and water, highlighting the necessity for a balanced approach.
Implementing Automatic Blowdown Systems
Technological advancements have allowed for more sophisticated blowdown processes, including the implementation of automatic blowdown systems. These systems offer real-time monitoring and adjustment of blowdown frequency, reducing the need for manual intervention while optimizing efficiency and resource use. Facilities that handle significant steam loads or complex operations benefit greatly from such automation, ensuring consistent performance without overburdening human operators.
Conclusion
Determining the optimal blowdown frequency for a steam boiler is a multifaceted decision that must account for water quality, boiler type, operating conditions, and the specific demands of the operation. Relying on expertise and consistent water testing forms the foundation of an effective blowdown strategy, ensuring the longevity, safety, and efficiency of steam boiler operations. By embracing technological solutions like automatic blowdown systems, facilities can further enhance their maintenance regimens, paving the way for reliable and optimized boiler performance.