Low pressure steam systems are critical components in various industrial and commercial settings, offering an efficient and cost-effective means of heat transfer. Despite their significance, understanding the intricacies of low pressure steam pressure can pose a challenge for many. From ensuring optimal system performance to guaranteeing safety and compliance, managing low pressure steam systems requires a blend of experience, technical knowledge, and attention to detail.
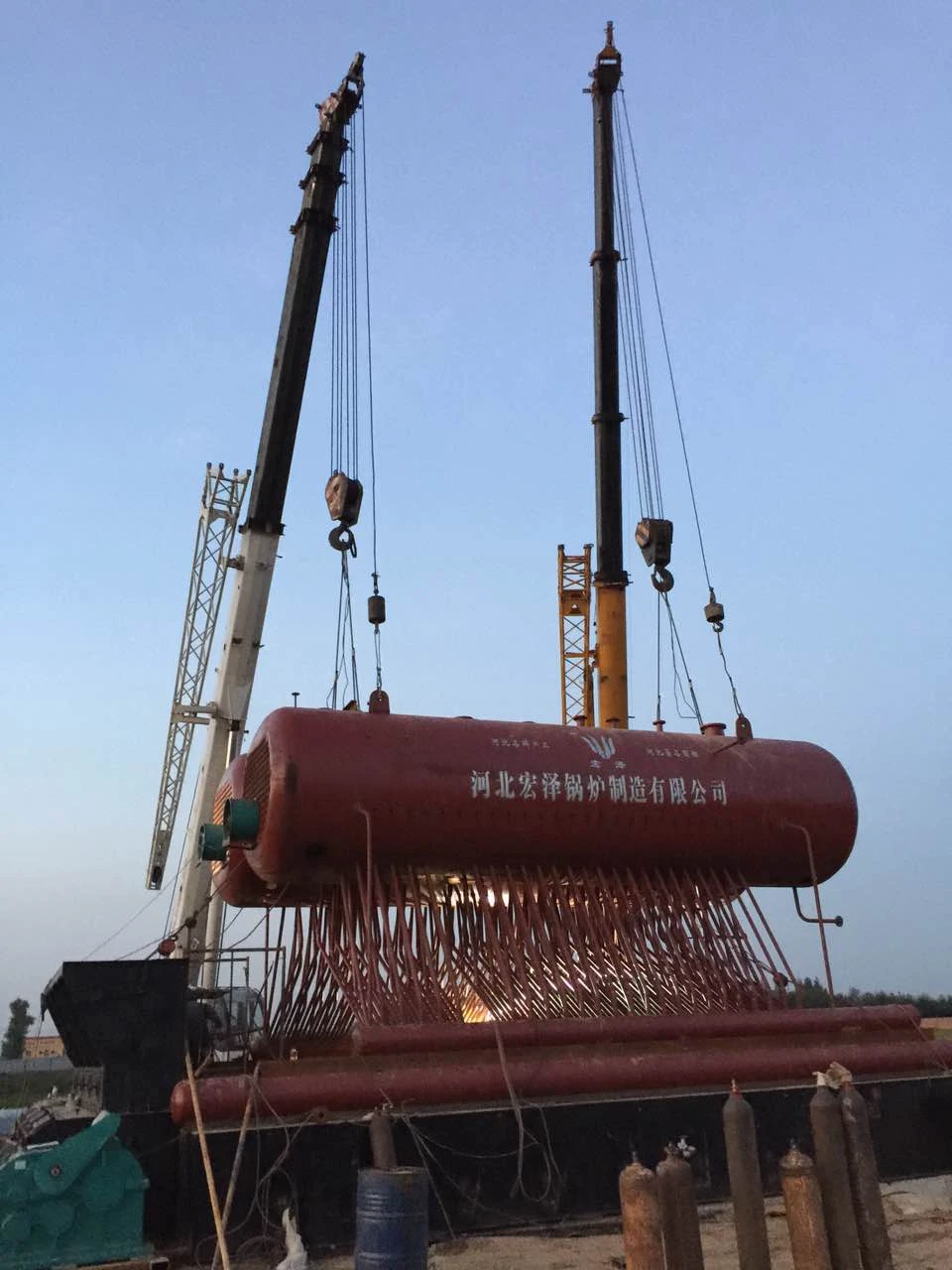
The fundamental concept behind low pressure steam systems involves generating steam at pressures typically below 15 psi, suitable for a wide range of heating applications. These systems are extensively used in industries such as food processing, textile production, and chemical manufacturing, where precise temperature control is essential. The lower pressure reduces the risks associated with high-pressure systems, making it safer for environments where safety is a paramount concern.
Expertise in low pressure steam systems is essential for optimizing system performance and ensuring longevity. One must have a comprehensive understanding of the core components, including boilers, heat exchangers, and pressure reducing valves. Proper installation and maintenance are crucial; if a boiler is not correctly calibrated, it can lead to inefficient operation and increased energy costs. Regular inspection of valves and pipes ensures that the steam system remains free from leaks, which can compromise system efficiency.
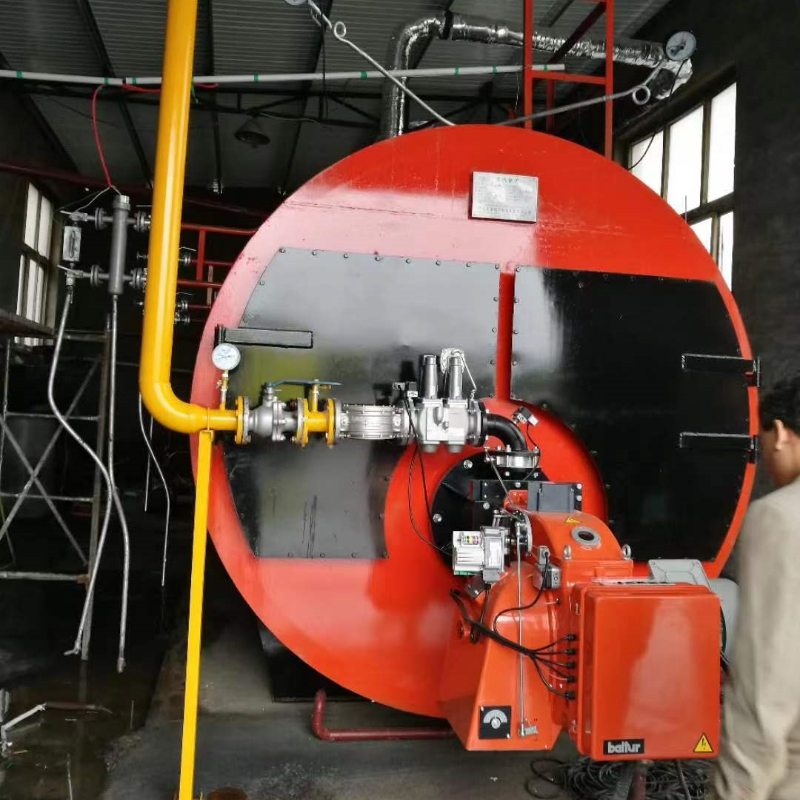
Authoritativeness in this domain comes from both theoretical knowledge and practical experience. Professionals working with low pressure steam systems need to stay abreast of the latest industry standards and safety regulations. This not only includes adherence to the pressure vessel codes but also understanding the environmental implications of steam generation. Reducing emissions and minimizing energy consumption are increasingly important in today's sustainability-focused world.
low pressure steam pressure
Trustworthiness in managing low pressure steam systems derives from transparency and reliability in operations. Operators should conduct routine system audits to verify performance metrics and implement corrective measures as needed. Utilizing technologies such as remote monitoring systems can enhance operational transparency, allowing for real-time data analysis and quick identification of potential issues. This proactive approach not only instills confidence in stakeholders but also extends the operational life of the steam system.
When considering the implementation or upgrade of a low pressure steam system, the selection of equipment and design should be guided by the specific requirements of the application. Custom-engineering solutions to fit unique operational needs ensures that the system is both effective and efficient. For instance, selecting the right boiler type, whether fire-tube or water-tube, depends on factors such as available space, fuel type, and desired steam output.
In sum, the management of low pressure steam systems involves a blend of practical experience, detailed technical knowledge, and adherence to rigorous safety and environmental standards. By focusing on these areas, industries can ensure the efficient, safe, and sustainable operation of their steam systems, thereby maximizing the return on investment and supporting broader operational goals. The continued evolution of technologies and methodologies in steam system management holds promise for even greater efficiencies and innovations in the future.