Enhancing the Performance of Steam Boilers with Advanced Pressure Switches
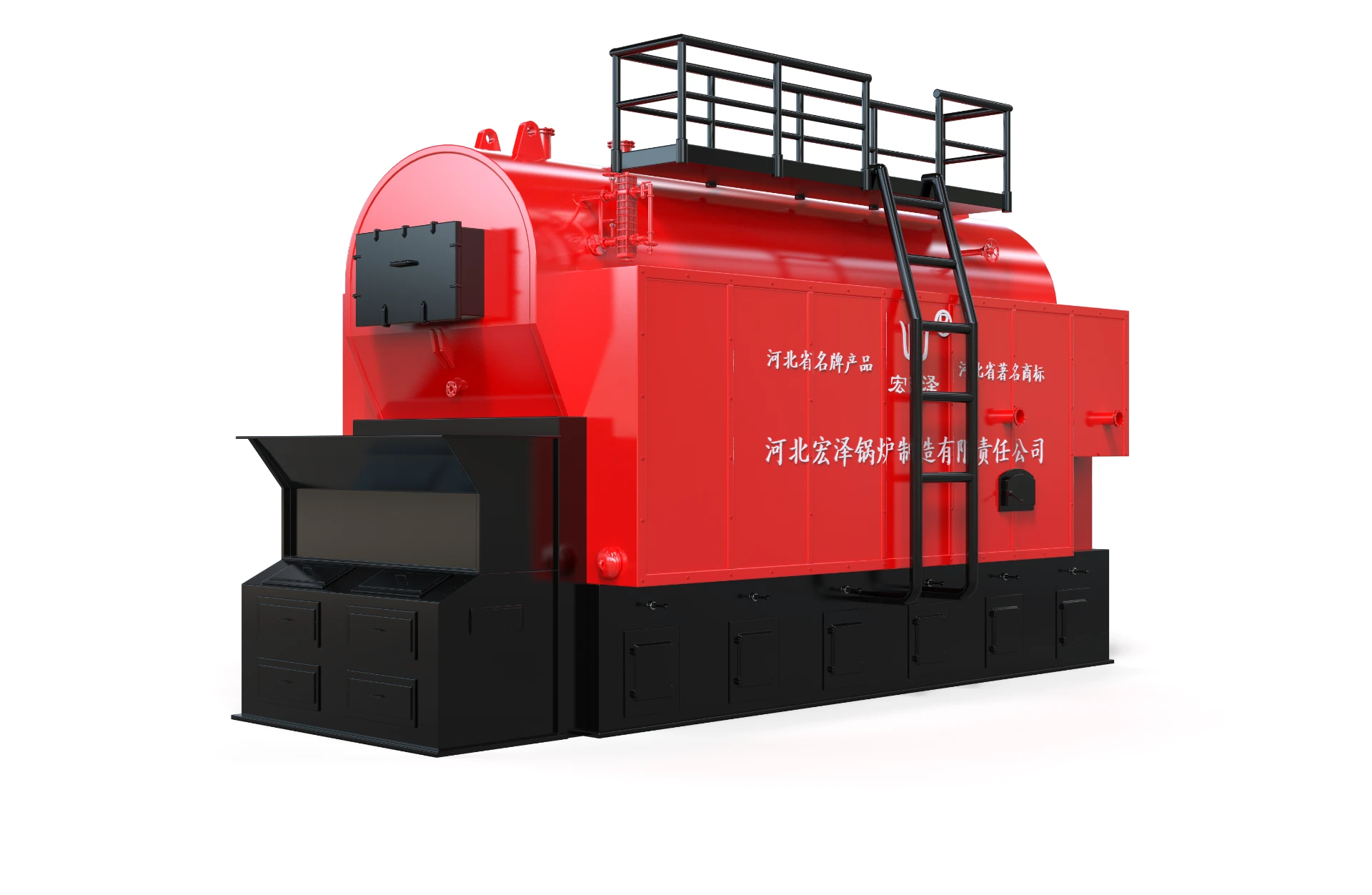
In the realm of industrial engineering, the steam boiler remains a critical component, responsible for a wide array of applications, from power generation to heating systems. A pressure switch in a steam boiler system is an essential yet often underappreciated element that ensures safe and efficient operation. This article delves into the intricacies of pressure switches in steam boilers, offering a granular insight into their functionality, types, and the reasons why they are indispensable in modern industrial operations.
Pressure switches are devices that sense changes in pressure and trigger corresponding actions. In the context of steam boilers, they monitor steam pressure within the system and act as a safety device to maintain pressure within permissible limits. The switch operates by making or breaking an electrical connection when the pressure rises or falls to a set level.

One of the most crucial aspects of pressure switches in steam boilers is their ability to prevent catastrophic failures. By continuously monitoring the pressure, they provide an automated means of pressure regulation, significantly diminishing the risk of explosion due to overpressure. This ensures not only the safety of the facility but also prolongs the boiler's lifespan, offering operators peace of mind.
Selecting the right pressure switch is a process that requires expertise. It is vital to consider factors like the range of pressure to be controlled, the type of media (steam in this case), the environment in which the switch will operate, and the boiler's specific operational demands. Pressure switches come in various designs, including electromechanical and electronic variants, each with its unique advantages. Electromechanical pressure switches are known for their simplicity and reliability, while electronic pressure switches offer enhanced precision and flexibility, suitable for integration into automated systems.
pressure switch steam boiler
In terms of real-world application, a common pressure switch type used in steam boilers is the differential pressure switch. This device measures the difference in pressure from two points in the system, providing a more nuanced control mechanism. Its role in optimizing both energy efficiency and operational safety is invaluable, making it a staple in many industrial setups.
To truly harness the benefits of pressure switches, proper installation and maintenance are non-negotiable. Misalignment or improper setup can lead to inaccurate readings, which compromise the safety and efficiency of the boiler system. Regular maintenance checks not only ensure longevity but also uphold the safety of the operations. Scheduled inspections and calibrations help in identifying issues before they escalate, thus maintaining an optimal balance between pressure levels and operational efficiency.
Standing out in the realm of pressure switch technology are brands such as Honeywell, Danfoss, and Ashcroft. These companies have established themselves as leaders through years of rigorous development and testing, reinforcing their authority and expertise in the domain. Their products are synonymous with quality and reliability, instrumental for engineers and industrial operators who seek performance without compromise.
In summary, pressure switches in steam boilers are more than just components; they are linchpins that underpin the entire operational framework of industrial steam systems. Their role in safeguarding operations, enhancing energy efficiency, and ensuring compliance with safety regulations cannot be overstated. For those in the market for pressure switches, the emphasis should be placed on expert consultation, quality brand selection, and regular maintenance practices. In a continuously evolving industrial landscape, the integration of such critical devices fortifies an organization's commitment to safety and efficiency. Through leveraging new technologies and maintaining industry best practices, businesses can ensure that their steam boiler systems operate at peak performance, with reliability and accuracy.